October is cybersecurity month, so we’re spotlighting the risks construction companies are now facing and how you can prevent them!
While this hasn’t always been the top concern for construction leaders, cybersecurity is quickly rising in the ranks as more and more construction firms are targeted in malware and ransomware attacks.
Why is construction a target?
Construction data doesn’t include the same amount of compromising client information as data from a bank might. While this seems like a good thing at first, it also means there are significantly fewer regulations around privacy and data security in the construction industry.
At the same time, technology is exploding with new possibilities for the future of construction. Without these important security regulations in place, however, these new technologies present a big risk to an enterprising construction tech company.
What are the 5 biggest risks?
- Phishing is when someone uses a fake email address, posing as someone trusted, to try to get information from your organization. Rushed employees might overlook the red flags and provide them what they need, compromising your organization.
- Domain imposters purchase domain names similar to your own or to a trusted partner, then email from them. Even if it’s someone you don’t recognize, the domain name creates a false sense of trust.
- Password guessing via computers can also be surprisingly easy, allowing a hacker access to a legitimate employee’s account. From there, a hacker can send emails or access sensitive information.
- Ransomware is the scariest of the bunch. After gaining access to your construction company’s system (possibly using one of the methods above), the hacker will block access and demand a ransom for operations to resume.
- Fraudulent wire transfers can also devastate a company. Using one of the above methods along with social engineering (manipulating people into doing what you want), an unsuspecting employee could transfer money to a hacker, all while thinking they were doing their job to keep the company running smoothly.
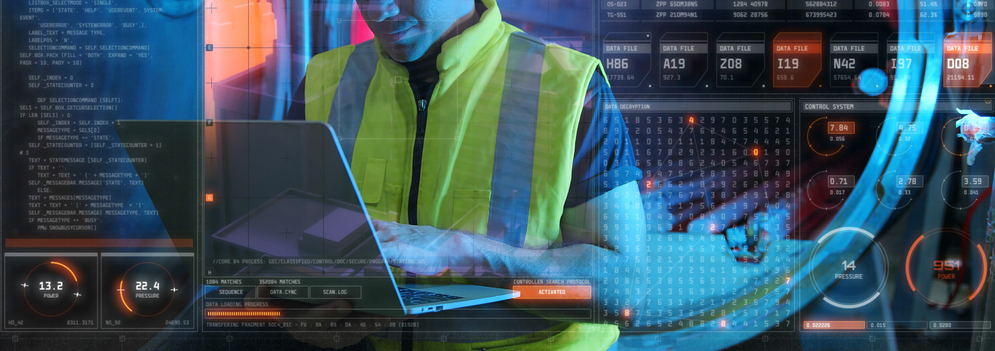
How do I protect my company?
You’re probably already very familiar with locking and securing your physical equipment. So now you need to learn how to be just as vigilant with your data.
- Learn about cybersecurity (by reading articles like this!) and stay on top of the latest hacking methods.
- Teach yourself and your staff to recognize suspicious domains and email addresses. Nothing is so urgent that you can’t double-check the sender’s request!
- Create strong passwords and enable multi-factor authentication.
- Set up cybersecurity software, like email spam filters and malware protection.
- Keep backups of all your data so you won’t be vulnerable to ransomware.
- Consider cybersecurity insurance or a third-party cybersecurity company.
Some of these protections can be set up in just minutes! Protecting yourself and your business is easy when you get in the habit of good security. Explore cybersecurity more at Cox Blue.