When you think of a construction project, you don’t always picture green trees and eco-friendly landscapes. Yet construction plays a big part in how we interact with the world and the impact we have on it. Construction projects develop the infrastructure of the future.
As technology improves and more countries buy into environmentally-friendly industry, construction gains new opportunities for better results and safer worksites. From biophilic designs to research into more sustainable (and more effective!) construction materials, construction leaders have the opportunity to make big, positive changes in their projects – and their bottom line!
AGC Report
Recently, the Associated General Contractors of America (AGC) released a 16-page report on the government’s incentives and investment into modernized infrastructure projects that incorporate key sustainability elements, like reducing waste, water usage, and energy consumption. The report discussed the many tax incentives and ways that modernized construction will be supported as we move into the future.
The AGC also shared several green strategy ideas in the report, including:
- Solar-powered trailers
- Energy-efficient lighting
- Carpooling
- Anti-idling policies
- Hybrid vehicles
- Engine retrofits
- Jobsite recycling
- Water conservation
- Paperless administration
- Renewable energy credits
- Green-certified office spaces
While these sustainability enhancements might seem like more trouble or money than they’re worth, streamlining operations and improving materials can actually save money and dramatically improve a company’s long-term viability.
One notable example is a company that instituted an anti-idling policy “to reduce fuel consumption, emissions, noise pollution and needless engine wear and tear.” By instituting this simple policy, the company saved more than $800,000 on just one project.
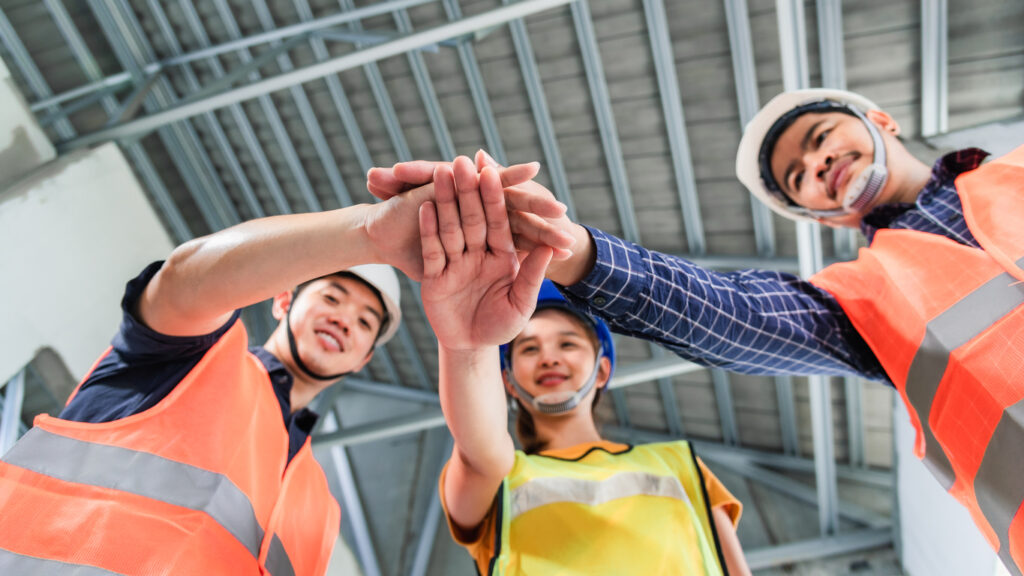
You Can Make an Impact
Whether you’re a CEO, a project manager, or an operating engineer, there are ways you can improve your impact on the environment at work. Some easy ways to get started include:
- Source sustainable and/or prefabricated materials
- Go paperless whenever possible
- Recycle materials when safe to do so
- Get the latest in energy-efficient equipment
- Track utilities and energy consumption
- Promote ridesharing, hybrid vehicles, and anti-idling policies
You can also share this article on your social media, tell your team about some of the ideas, or start brainstorming ideas that would work best for you. Together we can set up a better tomorrow for us all!
Steadfast is committed to sourcing modern, environmentally-friendly equipment and operators trained in sustainable operation. Give us a call to rent equipment or staff your next job: 1-855-449-0777.